Forklift Facts & Stats 2025: In-Depth Analysis of Accidents, Market Trends & Safety
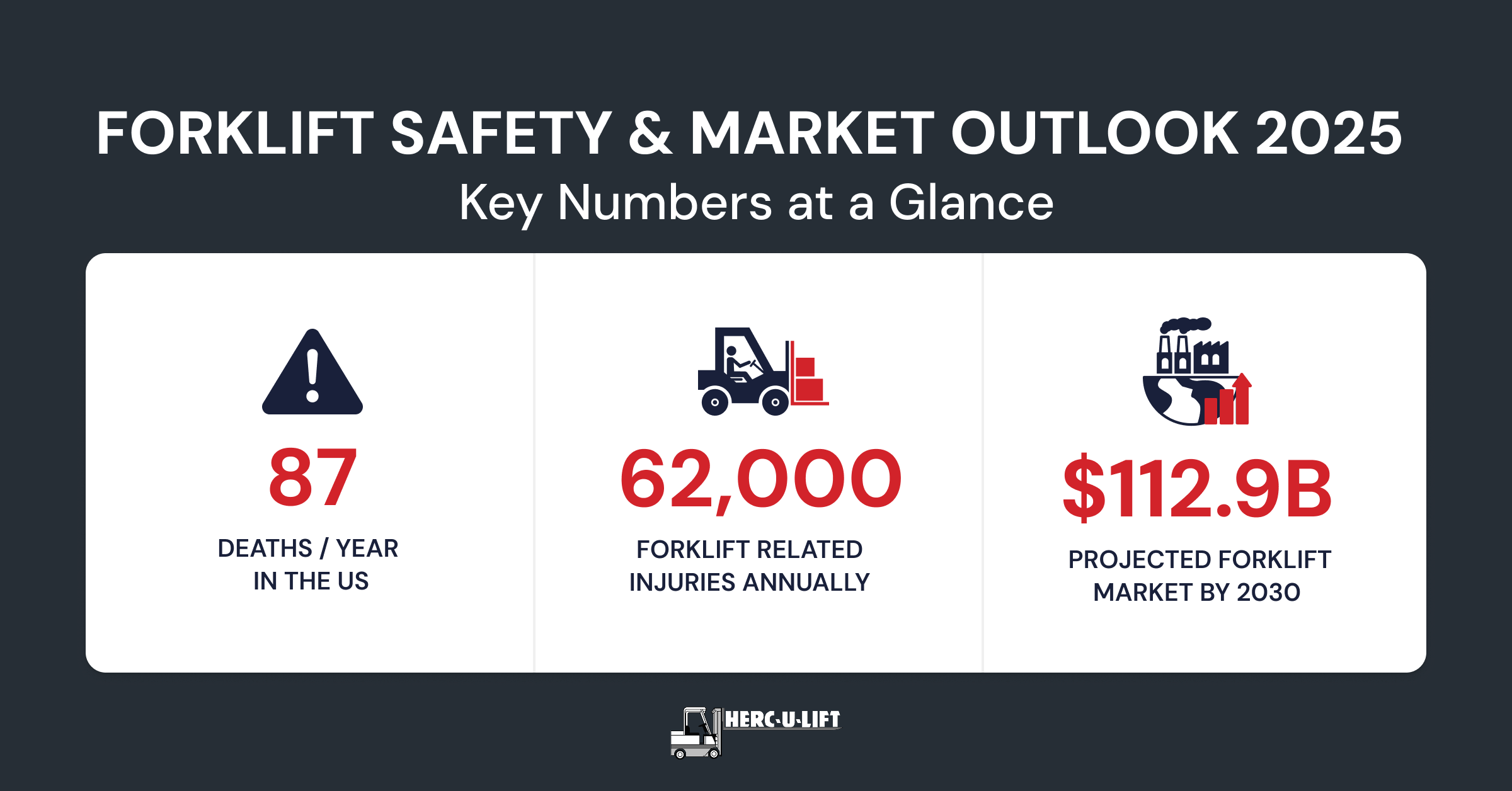
Forklifts have long served as the backbone of material handling operations. In distribution centers, construction zones, and manufacturing facilities, they move critical goods with precision and speed. Yet behind this efficiency lies an industrial reality filled with risk.
Every year, thousands of workers are injured in forklift-related incidents. Some result in damaged equipment or lost time while others cause serious injuries. The costs aren’t only measured in dollars, but in lives affected.
This review isn’t just about numbers. It’s a reality check. We’ll walk through the most recent forklift accident statistics. We even look at where and why these incidents happen in the first place. Also, we explore the latest market trends and break down the safety protocols and tech that can help prevent such incidents.
Accident Overview: The Raw Numbers
The latest data from U.S. and global safety agencies show forklift accidents remain far too common. In the United States alone, an estimated between 35,000 and 62,000 forklift-related injuries occur each year. Roughly 34,900 of these are serious enough to involve fractures, crush injuries, or permanent damage.
Worldwide, forklift injuries total around 96,700 cases annually. And in the U.S., an average of 87 workers lose their lives each year to forklift incidents. While that may not sound like a huge number compared to other workplace hazards, each one represents a preventable loss and a failure somewhere in the system.
Breakdown of Accident Types:
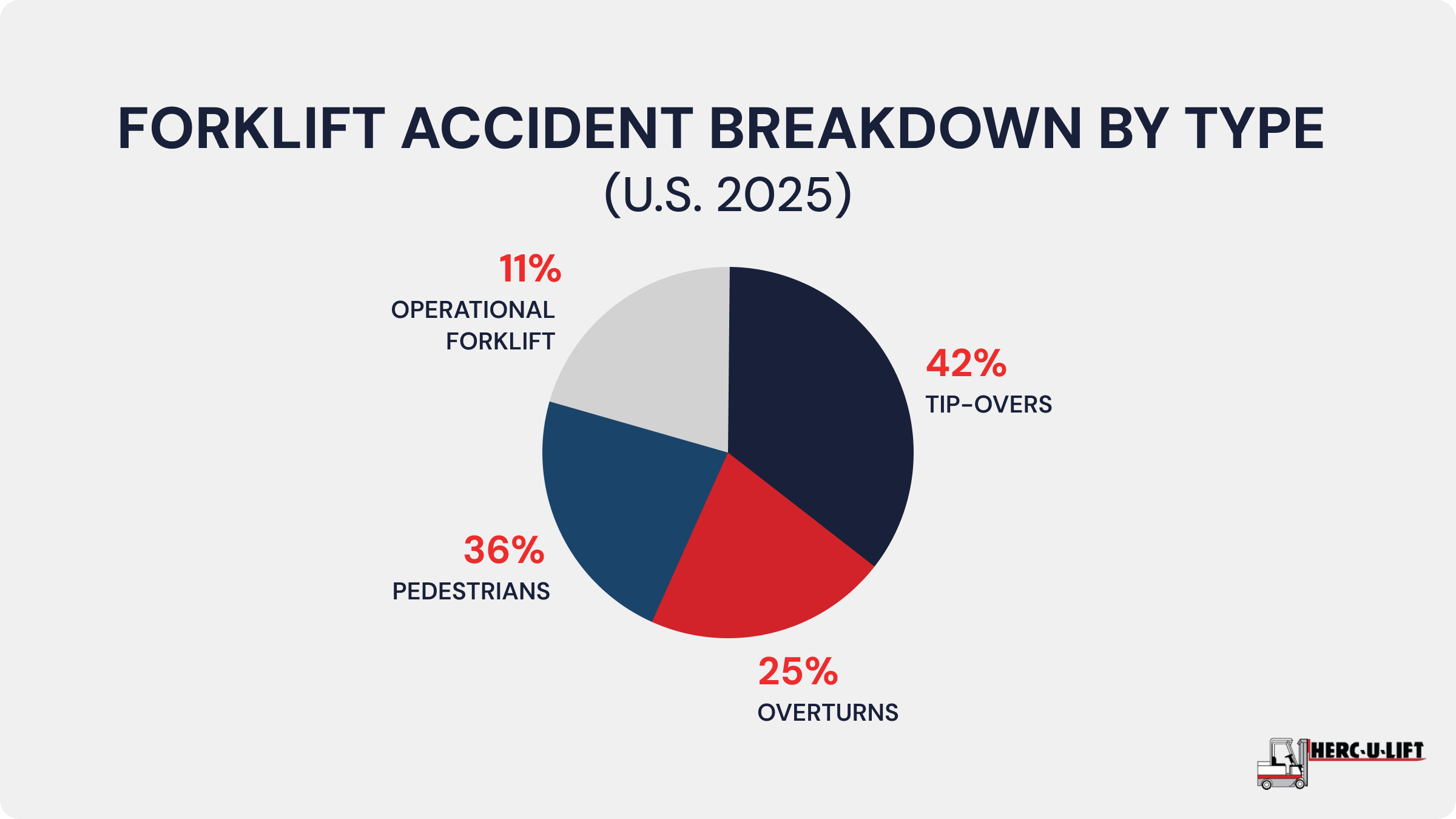
These statistics provide clarity. They’re warning signs telling us what the biggest risks are.
Accident Hotspots and Risk Factors
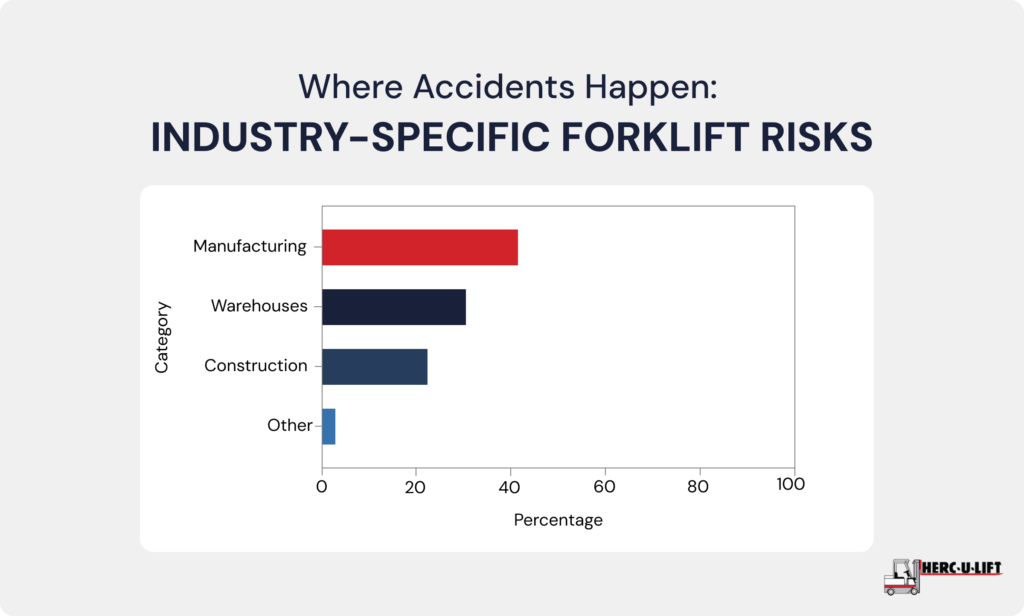
Forklift hazards aren’t tied to one specific industry. However, some environments are more accident-prone than others. Case in point, warehouses represent nearly 30% of all forklift-related accidents in the United States. The tight aisles, heavy foot traffic, and blind spots create a constant mix of machinery and pedestrians – a recipe for risk.
Looking at industry-specific data gives us a clearer picture:
Operator fatigue is another major factor. Long shifts (10 to 12 hours or more) don’t just make people tired. They also slow reaction times, cloud judgment, and increase mistakes. Fatigued workers are 37% more likely to get hurt. On a 9,000-pound machine, one small miscalculation can have big consequences.
The Financial Toll of Forklift Accidents
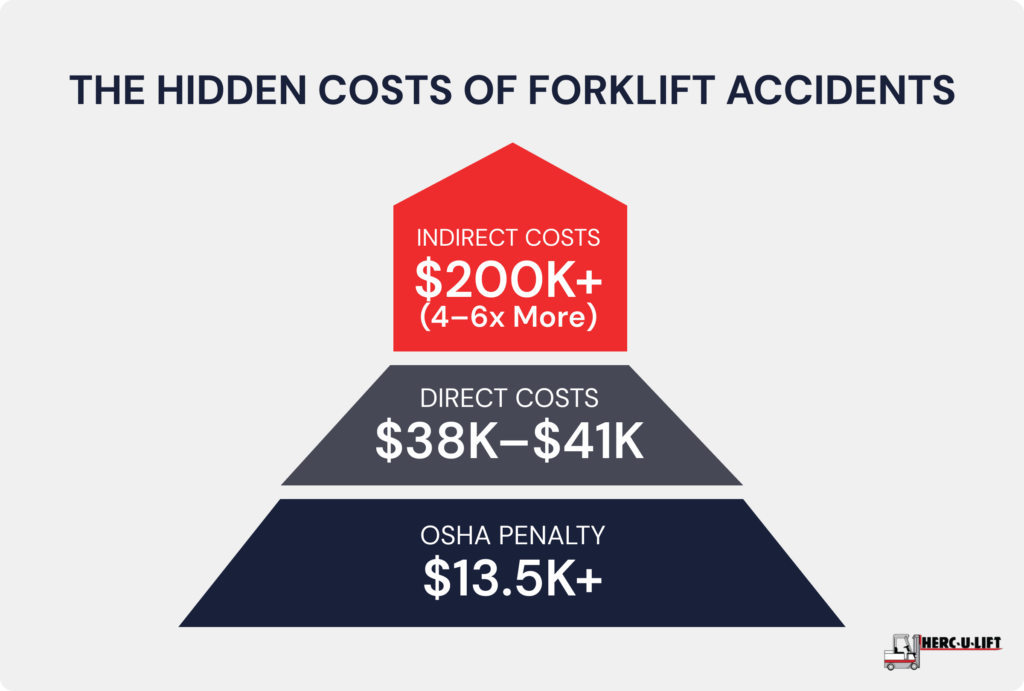
The human cost is clear, but the financial cost can also be staggering. A single workers’ compensation claim for a forklift injury averages $38,000 to $41,000 in direct costs. In addition, an OSHA violation often costs $13,500 per citation.
Yet these numbers only scratch the surface.
But that’s just the surface. The indirect costs (lost productivity, damaged inventory, legal fees, replacing injured workers, higher insurance premiums) can be four to six times the direct cost. That means a major incident can easily top $200,000 in total impact.
For some companies, one serious accident is enough to throw off an entire year’s profit targets.
Why Forklifts Present Unique Hazards
Forklifts do not behave like regular vehicles. They’re designed to lift, not to be inherently stable.
Key risk factors include:
Weight
Standard models can weigh up to 9,000 pounds. They’re significantly heavier than cars or pickup trucks.Speed
Some models can hit 18 mph in warehouse settings.Weight distribution
Rear-mounted engines and front lifting mechanisms make them front-heavy.Visibility
Loads can obstruct forward view, especially when lifted. Side and rear visibility is also compromised in narrow aisles.Steering mechanics
Rear-wheel steering helps with tight turns but increases the risk of swing-outs and over-rotation.Braking limitations
Forklifts primarily rely on front braking systems. This can delay stopping under load or on inclines.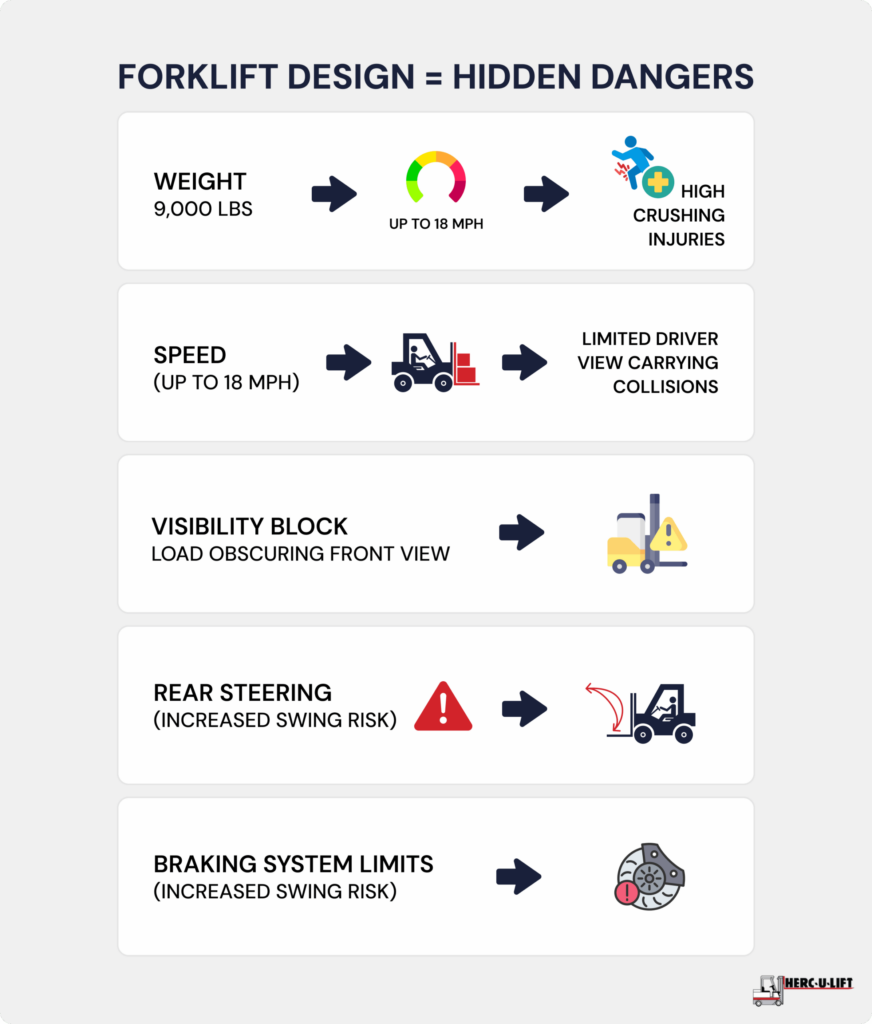
These design traits mean forklift safety isn’t just about driving carefully. It’s about understanding how the machine’s physics work and adjusting your operation accordingly.
Market Trends: Electric Forklifts Take the Lead
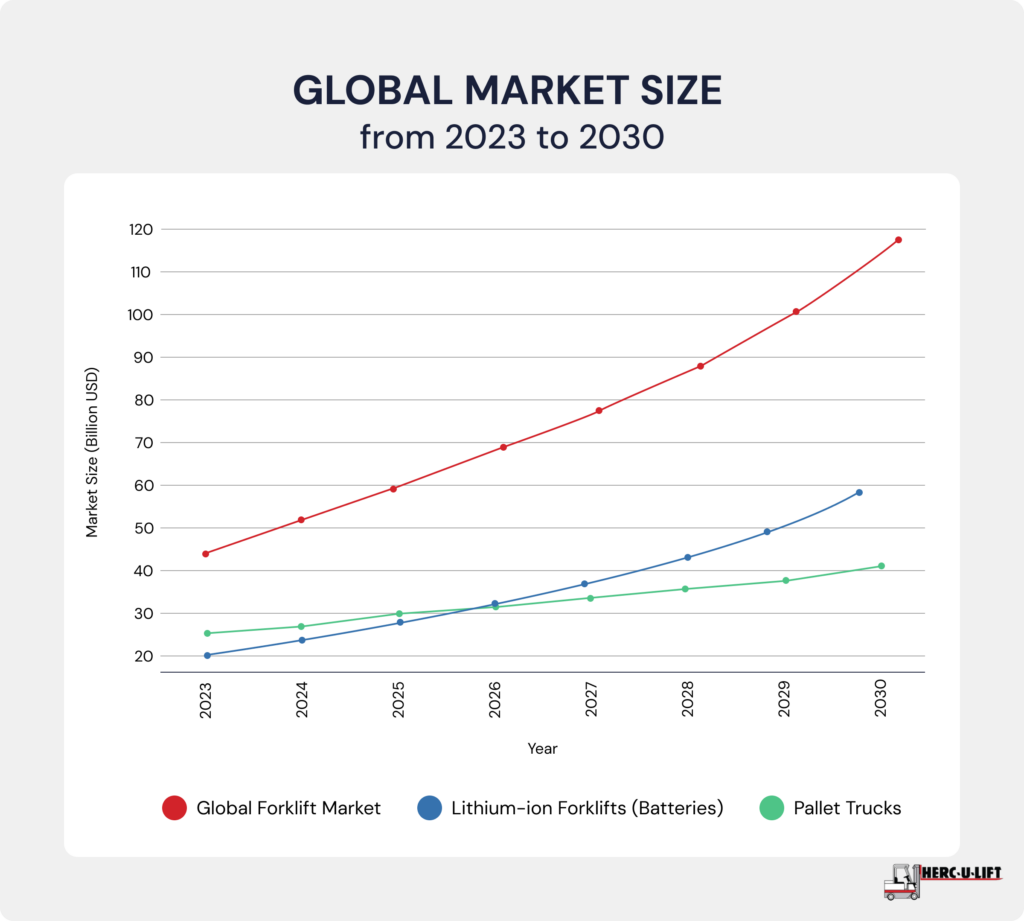
The forklift market isn’t standing still. In 2023, it was valued at USD 45 billion. 2030 market projections indicate it could reach US $112.9 billion, with a 14.4% compound annual growth rate (CAGR).
Four areas are leading this shift:
Battery Technology
Lithium-ion batteries, worth about $20.2 billion in 2023, are becoming the norm. Their low maintenance and rapid charging features appeal to a growing demographic. Meanwhile, hydrogen fuel cells are also gaining traction for operations that need long run times and quick refueling.Application Growth
The demand for pallet trucks is growing, with 28.4% of total units sold. This is particularly evident in sectors like e-commerce, last-mile delivery hubs, and grocery fulfillment centers.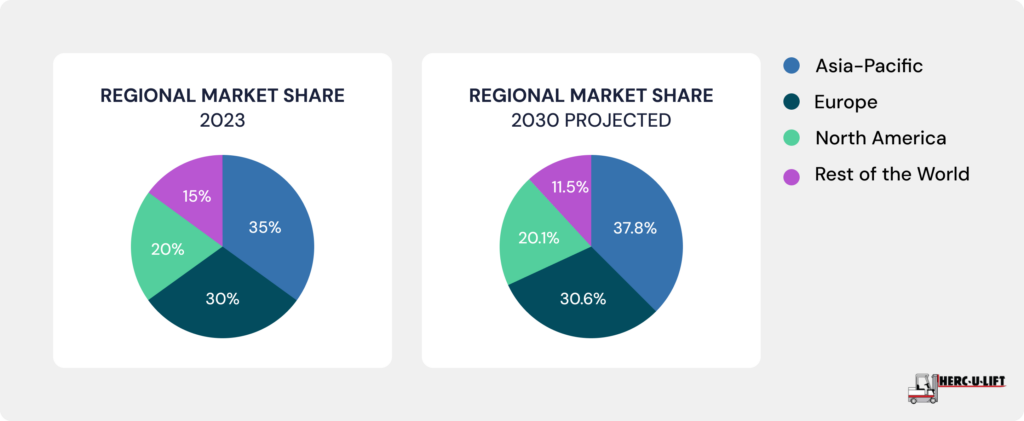
Geographic Expansion
While Europe leads in revenue, growth in North America (CAGR 12.2%) and Asia-Pacific (CAGR ~15.9%) is accelerating rapidly. This trend is driven by regional investments in warehouse automation and smart manufacturing.Rental Growth
Companies are increasingly renting forklifts to access the latest models without heavy capital investment. Short-term leases help cover seasonal demand or project-based logistics.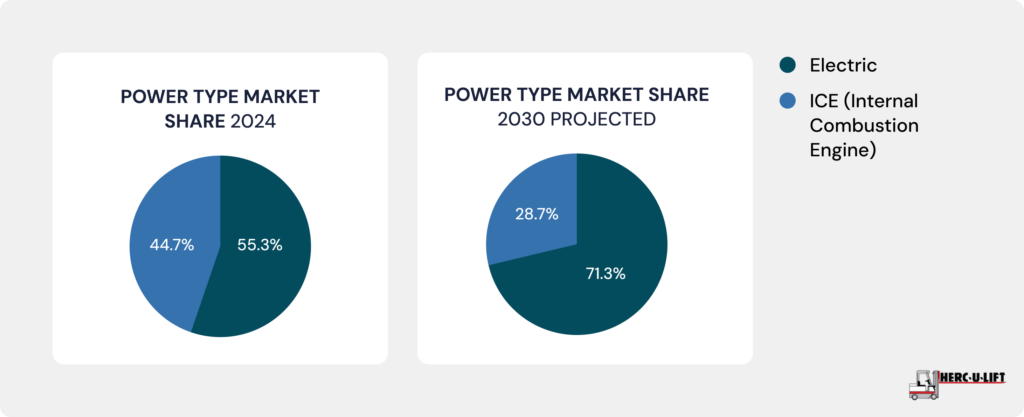
Prevention: Modern Safety Protocols and Emerging Solutions
Safe forklift operations don’t just happen. They’re built through proactive measures. You shouldn’t for compliance mandates or post-incident reviews. Prevention strategies today are increasingly data-driven and technology-supported.
Training shouldn’t stop at certification. Regular evaluations and continuous practice keep skills fresh and safety standards high.
If you oversee forklift operations, audit your current training protocols. Make sure your team isn’t just certified but are truly prepared. Investing in ongoing training today could save lives tomorrow.
✓ Brake system
✓ Hydraulic lift components
✓ Steering mechanisms
✓ Tire integrity
✓ Safety belt function
Skipping even one of these checks is gambling with safety.
✓ Limit shift durations to 8 hours.
✓ Enforce speed limits in high-risk areas.
✓ Install physical barriers and designate separate walkways for pedestrians.
✓ Equip machines with ample lighting, warning alarms, and rear-view mirrors.
These controls create layers of defense that reduce both the frequency and severity of incidents.
Real-World Impact: What the Numbers Reveal
The good news? These trends can change. The solutions are known. The technology exists. And every company has the choice to treat forklift safety not as a box to check, but as a culture to build.
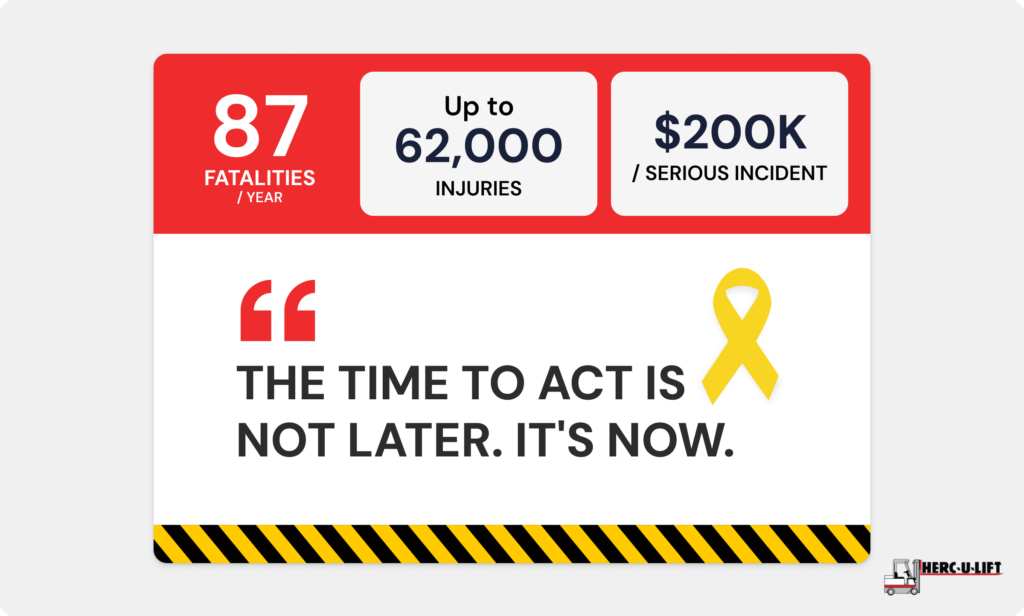